电气控制系统在整条电机绕线与装配生产线中,堪称“大脑”与“中枢神经”,是确保装备高效、精准、稳固运行的焦点所在。它不但统筹协调了整个装备的行动流程控制和各个工序之间的衔接,更肩负着实时监测、数据收罗与异常反响的重任,为产线的顺畅运行提供了坚实包管。

详细而言,电控系统通过编程实现了各环节的自动化指令,好比绕线张力控制、绕线头切换、槽位定位、压接力度调理以及装配历程中的同步行动。这些行动流程的背后,依赖于PLC、HMI、伺服驱动器、传感器等焦点部件的协同控制。而电控系统正是将这些硬件“有机整合”为纽带,确保每一步行动既高效快速,又坚持误差最小化,阻止产品不良率的爆发。
别的,现代电气控制系统已经不再局限于“基础行动控制”,更在智能化、数字化偏向一直升级。例如,合利士接纳的数据收罗?榭墒凳奔嗫氐缌鳌⒌缪埂⑽露取⒄帕Φ纫ひ詹问,团结上位机或MES系统,做到生产数据的可追溯、报警信息的实时推送、产能统计的自动剖析。这样一来,不但提升了整条产线的治理透明度,还利便客户举行远程维护与决议优化。
更主要的是,一个设计合理、架构清晰的电控系统,能够显著降低后期维护本钱。合利士团结多家PLC品牌及客户需求,提前为系统预留扩展接口和功效升级空间,阻止客户在未来需要新增功效或顺应新型号时,面临整系一切重构的困扰。
同时,通过标准化的程序?椤⒂押玫牟僮鹘缑嬉约跋晗傅牟僮魉得,使得一线手艺职员即便没有高级编程配景,也能轻松掌握装备操作和简朴参数调解,降低对高手艺人才的依赖。
汽车、电机与高端制造行业痛点(一)
在汽车、电机与高端制造行业中,自动化装备的普及虽然带来了生产效率的整体提升,但随之而来的电控系统设计与调试问题,却成为许多企业亟需解决的瓶颈。尤其在电机绕线和装配环节,客户对生产一致性、稳固性、良品率提出越来越高的要求。
然而,面临装备个性化需求一直增添、产线工序多样化、交期日益主要;古板电气控制系统往往难以同时兼顾定制无邪性与系统稳固性。
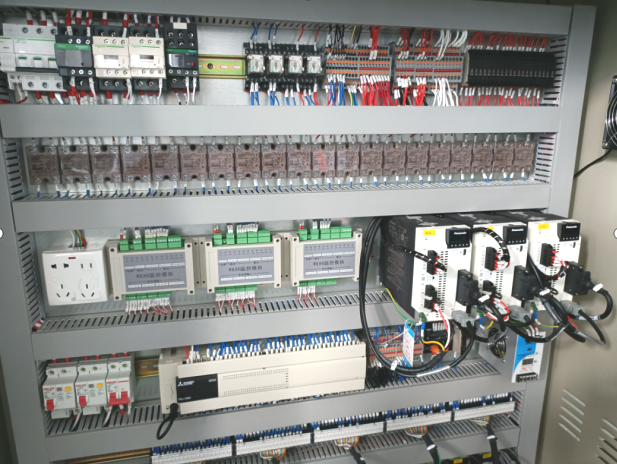
电机自动化装备的开发周期普遍较短,每套生产线的功效、结构、客户工艺要求各不相同,导致开发比例高、定制化水平高。工程师们在短时间内需要完成电控计划设计、程序开发与现场调试,这无疑加剧了蜕化率,BUG频发,返工或修改本钱高。
而电气控制系统自己敌手艺水平要求极高,不但需要具备富厚的PLC编程履历,还要对差别PLC品牌如西门子、三菱、欧姆龙等的编程语言与通讯协议熟悉掌握,使得企业对电气工程师人才的依赖度居高不下,人才作育周期长,难度大。
汽车、电机与高端制造行业客户难点(二)
从客户角度来看,电机生产现场工况重大,涉及张力控制、多轴联动、视觉检测等多种工艺,导致后续程序调试与修改十分难题。
尤其是当产线交付后,客户在后期遇到装备参数调解、功效升级或故障排查时,往往受限于控制程序不透明、品牌兼容性缺乏、售后响应不实时,极易泛起生产障碍,甚至影响交货?突毡槊媪“售后支援难”、“调试周期长”、“系统维护依赖原厂”等这一系列痛点,严重制约了产能释放和本钱控制。
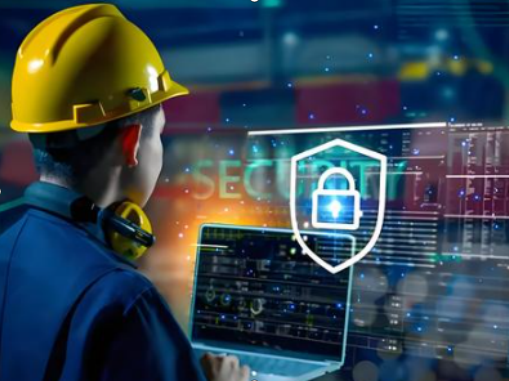
正因云云,企业亟需一套既能知足高度定制化需求、又能降低系统开发与调试门槛,同时兼具开放性与易维护性的智能电气控制系统,以真正解决电机绕线与装配历程中的质量控制和生产效率难题。
|